Fixed chamber baler
Round baler | G-1 F125
The G-1 F125 is an absolute professional machine with maximum output.
The fixed chamber baler is extremely robust and has been developed for all possible applications - whether silage, hay or straw - dry or wet - the round baler is equipped for all situations.
Highlights of the fixed chamber baler
Pick-Up
The starting point of every firmly compressed round bale is the clean pickup of the base feed: Its pendulum suspension allows the 6-row pendulum pickup to deliver maximum conveyance capacity along with superior ground adaptation and enables it to absorb even the largest swaths without a hitch.
Pendulum-Pick-Up
The suspended installation in a central position creates a swing range of 150 mm. It provides for top-notch ground adaptation and compensates for any unevenness in the terrain with perfect ease. Doing without a cam track, the pendulum pickup offers a DIN rake width of 2.20 m and large conveying screws on the sides that guarantee an optimum flow of material to the rotor. Equipped with tines spaced 51 mm apart across six rows, the pickup delivers firstrate raking performance even when handling extremely wide swaths.
Plastic Strippers
Another unique feature are the plastic strippers. Exceptionally resilient, these strippers withstand even the greatest amount of stress and will not bend if colliding with foreign objects. Stripping the material off with great efficiency, the tines also enhance the flow of material.
Twin Roller Holding-Down Devices
Comprised of twin rollers, the standard holding-down devices with a new suspension boost the material flow even when dealing with uneven swaths and fill the bale chamber in a continuous and uniform manner.
Smoothly Running Touch Wheels
Fitted with pneumatic tires, the touch wheels work in perfect harmony with the pendulum pickup and run with maximum smoothness. Adjusting the height of the touch wheels is quick and easy thanks to perforated rails that eliminate the need for any tools. Customers can also opt for swiveling touch wheels.
Feeding System
Short and precisely cut feed is the basis for the production of high-quality and high-energy silage. The material in the GÖWEIL baler flows through its own special passageway – the rotor! This feeding system guarantees optimum feed pick-up under all sorts of harvest conditions.
One rotor for all harvest conditions
Fitted at the heart of the feeding system is a 6-star rotor that offers enormous absorption capacity. Thanks to its large diameter of 570 mm and the welded-on rows of HARDOX tines, the rotor will always cut the swaths of feed cleanly and convey them reliably into the bale chamber – whether they are large and dry or contain feed that is short and still wet. Installed in front of the rotor is a mechanically powered infeed roller. Precompressing the material with outstanding efficiency, the roller increases the throughput significantly. The newly developed starter roller housed in the bale chamber provides for optimum bale rotation and a reliable start.
Perfect flow of material
The rotational direction of the rotor built into the G-1 F125 is upward. This movement channels the material from the rotor through the cutting unit and into the bale chamber.
Drop floor & Cutting unit
As the cutting unit is positioned above the rotor, changing the blades is a breeze and can be accomplished without any tools. This offers an advantage that is particularly beneficial in baler-wrapper combinations. The cutting unit is fitted with 30 twin-blade cutting edges and makes it possible to achieve a cutting length of 35 mm. The narrow spacing between rotor tine and knife ensures that the feed is chopped with pristine accuracy. The replacement knife bar allows the operator to carry along 30 replacement knives or change the number of cutting knives as needed. A hydraulic bar safety device protects the knives against foreign objects and moves them immediately into their cutting position.
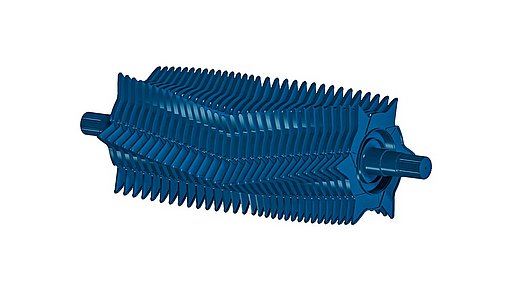
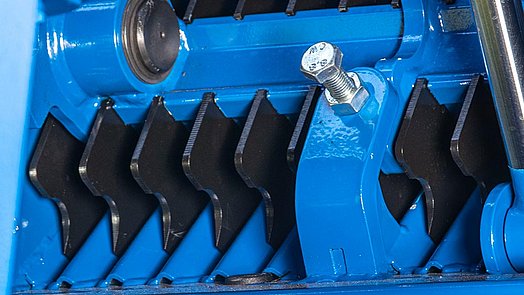
Auto-Flow-Control (AFC)
The AFC (Auto Flow Control) monitors the entire flow of material and intervenes in fully automatic fashion as soon as detecting a problem in the conveying duct. This ensures that clogs at the rotor or pickup are removed fast and without effort! Here is how it works:
Unclogging the Rotor
The rotor’s overload safeguard trips whenever the conveying duct for the quantity of feed to be delivered becomes too narrow. The hydraulic top floor opens towards the top, and the knives flip back.
When the rotor starts up again, the excess material is guided unobstructed into the bale chamber. The drop floor and the knives subsequently return to their original positions, allowing the feed pick-up to resume without hindrance.
Unclogging the Pick-Up
An overload safeguard will also be tripped if too much feed has accumulated at the pickup. Normally powered mechanically, the infeed roller will then be briefly driven and supported hydraulically to allow it to keep conveying the material. Concurrently with the infeed roller the drop floor swivels up, allowing the material to find its way directly into the bale chamber.
Bale chamber
At the core of the machine is the bale chamber, which offers a size of 1.20 m x 1.25 m as well as 18 solid forming rollers. The steel rollers are 4 mm thick and reinforced on the inside, while their ribbed profile ensures supreme compression density and the reliable rotation of the bale.
Bale chambers & Co
Two drive rollers with a shaft diameter of 65 mm and the additional roller shafts with a diameter of 60 mm run continuously on double-row pendulum roller bearings and provide for exquisite stability and an exceptionally long lifetime. A specially designed labyrinth prevents dust and dirt from penetrating.
Starter & Cleaning Roller
Situated directly behind the rotor, the starter roller provides for the best possible bale rotation and a reliable bale start thanks to its special profile – whether the material is silage, hay or straw. A cleaning roller feeds any material that has dropped down back into the bale chamber – keeping the machine from becoming soiled.
Tailgate
The tailgate opens and closes with the help of two hydraulic cylinders. Depending on the program setting, the process will be completed automatically or manually.
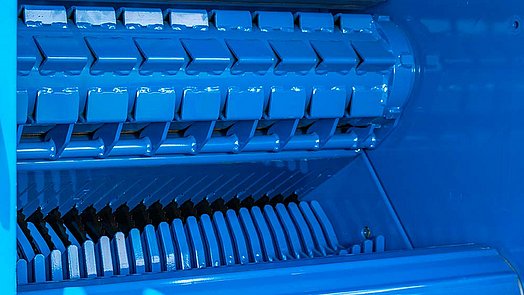

Bale catcher
The patented bale catcher allows for the fully automatic catching of the bale, preventing the bale from rolling away uncontrollably when dropped in steep slope positions. The bale catcher eliminates the need for stopping the bale manually using the tailgate to prevent the bale from rolling away when it exits the bale chamber.
Silage additive dosing unit
The dosing unit uses two spray nozzles to add lactic acid bacteria to the silage, thereby enhancing its quality even further.
The silage additive dosing unit can be calibrated for acids of different viscosity. The driver stays in control of the quantity thanks to an inspection glass and a display.
Consisting of: 100 l tank, 2-point extraction (complete emptying) LSP junior NK (acid-resistant), pump with filter, electronic flow meter Dosistar VD 390, two nozzles 0.1 in stainless steel design.
Film- & Net binding
The round baler is equipped with film and net binding as standard. In addition, a dual binding unit is available for film and net.
Film binding unit
The use of a wide film offers decisive advantages that enhance the quality of the silage:
- A wide film produces bales that are more compact and better protected by the film layers. This film also provides an additional barrier preventing oxygen from penetrating.
- Opening and recycling the bales becomes easier as the wide and the wrapping film can be disposed of jointly.
The operator can insert common wide films and nets with a width of up to 1.50 m. Binding can be started automatically or manually. The hydraulically adjustable brake roller ensures that the bale is wrapped tightly during net and film binding. The brake pressures and the number of layers can be set directly using the control.
Twice the binding in half the time
Equipped with the world’s first dual binding unit, the G-1 breaks new ground for round balers. This optional binding system wraps the finished bale simultaneously in two nets or wide films. The result: This feature cuts in half both the time required for binding the bale and for changing the net or film! Reducing the workload significantly, this time savings will be much appreciated especially on the busiest days of the harvest. If the operator needs to alternate between silage, hay or stray bales on the same day, the machine offers them the option of using the dual film binding unit as a single binding unit. In this case, the dual binding unit is loaded with one net roll and with one roll of film. The operator simply uses the terminal to set one binding unit up for net binding or the other unit for film binding. Changing the film or the net does not cause any unnecessary idle time!
Drive axle
Round baler for mountain areas
Available as additional equipment, the drive axle is of tremendous benefit especially during work in steep slope positions. It provides a powerful, yet soil-preserving push uphill, while supporting the braking action during downhill travel. The driver can concentrate fully on the work.
The drive axle offers maximum safety and superior comfort in any slope position – uphill and downhill.
The sensor system integrated in the drawbar controls the operating states – Drive, Neutral, and Brake – in a completely autonomous way. The driver can rely on the system providing maximum traction at maximum soil protection, allowing them to solely concentrate on their work. A clearly organized display continuously informs the driver of all relevant parameters.
The drive is powered hydraulically by two radial piston / wheel hub engines. The switch between forward and reverse is initiated automatically by a signal given from the tractor. The percentage of the driving force with which the drive is supposed to power the machine in first and second gear is controlled via the terminal.
When the machine is driving uphill – either in reverse or forward – the drive switches automatically from drive mode to hydrostatic brake mode. To prevent the wheels from locking up, the speed of the two drive wheels is constantly monitored and readjusted automatically. This ensures that the wheels are constantly in motion during uphill travel (ABS).
When the machine is traveling on the road, the radial piston engines are automatically released mechanically and will freewheel (no mechanical resistance).
Drive
GÖWEIL's split drive concept ensures that the "Automatic Flow Control" (AFC) runs smoothly and guarantees a particularly high throughput rate.
No Downtime!
The power transferred by the PTO drive shaft to the main gearbox is spread across the drive chains of rotor, pickup and bale chamber and safeguarded individually by two cam switch couplings. The couplings are monitored by the ISOBUS program control.
When the cam switch coupling of the rotor responds to an excess quantity of feed in the conveying duct, the hydraulic drop floor will open in fully automatic fashion. When the rotor starts up again, the excess feed is guided unobstructed into the bale chamber. The drop floor closes automatically, allowing the baling process to resume without hindrance.
When the cam switch coupling responsible for the bale chamber trips, the tailgate will open automatically by a few centimeters and allow for the bale to be started and bound without hindrance.
The drive train conceived by GÖWEIL provides for a smooth work flow.
Maximum performance thanks to high-tensile chains
High-quality components are an essential prerequisite for the drive train’s smooth and trouble-free operation. The chains used for the main drive and for driving the pickup and the rotor in the machines of the latest generation have been increased in size yet again in order to boost the performance of the drive system even further. This extends the lifetime of the machine considerably and reduces the operation costs to a minimum.
Well-built roller bearings
All baler rollers are fitted with sturdy and durable double-row pendulum roller bearings with a diameter of 60 mm. Additionally, the two drive rollers are equipped with 65 mm bearings.
ISOBUS Control
Isobus is an internationally standardized protocol that is in charge of the communication between the tractor and the mounted implements. It allows for the real-time display of the data on the terminal housed in the tractor. The operator uses the terminal to monitor and control the machine. A standardized plug connection system has now eliminated the need for using more than one terminal for different implements.
GÖWEIL is making this baler generation available with ISOBUS as the standard option. The interface of the control is clearly arranged and easy to use. What is more, the color display shows a greater amount of information. The camera system affords the operator a good view of the work flow and the machine.
GÖWEIL offers customers a choice between two terminals:
- 4.3" touch display with 8 buttons and encoder (turn-and-push button)
- 7.0" touch display with 12 buttons and encoder (turn-and-push button)
The machines are, of course, compatible with all other ISOBUS-capable terminals. For tractors without ISOBUS, there is an optional wiring harness for ISOBUS-capable power supply available.
ISOBUS monitors and controls the entire work flow in fully automatic fashion. The clearly organized display keeps the driver informed about all steps processed by the machine. It is also possible to control all relevant work steps of the machine – quickly and easily – by hand using the terminal.
The control unit with push buttons used for the G-1 F125 Kombi comes in particularly handy when the wrapper requires maintenance and servicing. This way, the operator can control the most important functions directly at the machine.
Maintenance
A standard feature on the machine, the automatic central lubricator is designed to deliver superior ease of maintenance and ensures an exceptionally long lifetime for the machine.
Maintenance-Free thanks to central lubricator
The fully automatic grease lubricator is used to supply sufficient lubrication to all bearings of the rollers and of the rotor. The oil lubricator provides a constant supply of oil to all chains on the bale chamber, the rotor and the pickup. Brushes spread the oil evenly across the chains.
Sufficient Supply
The large-size reservoirs for grease and oil provide for long service intervals.
Basic Model
with EU type-approval
Load sensing (can also be operated in conjunction with tractors without load sensing pump)
- Camless pendulum pickup
- DIN rake width: 2.20 m (7’ 2”)
- Rows of tines: 6
- Tine spacing: 51 mm (2”)
- Plastic strippers
- Twin rollers
- Touch wheels with pneumatic tires
- 6-star rotor
- Hydraulic drop floor
- Cutting unit with 30 twin blade reversible knives
- Cutting length: 35 mm (1 3/8”)
- Hydraulic bar safety device
- 18 steel rollers (4 mm) reinforced on the inside (including cleaning & starter roller)
- Double-row pendulum roller bearings
- Net binding
- Hydraulically adjustable brake roller
- Automatic monitoring
Rigid drawbar
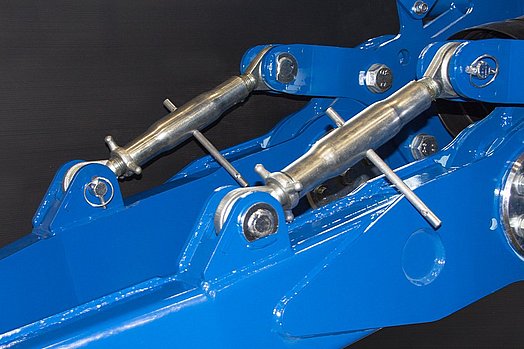
- Single axle
- Tires: 500/60-R22.5 FL630 Plus
- Brake system: dual-line air brake system
- PTO speed: 1,000 rpm
- AFC Auto Flow Control: split drive concept
- Overload safeguard with 2 cam switch couplings
- Chains:
- Main drive – bale chamber: 24 OH
- Secondary drive of bale chamber: 100 HSP
- Rotor: 80 HSP Triplex
- Pick-Up: 80 HSP
- Fully automatic central lubricator for grease and oil
- Fully automatic ISOBUS program control (without touch display)
Technical data (Basic model)
Height – single binding unit |
|
Height – dual binding unit |
|
Length | 4,735 mm (15’ 6”) |
Width (500/60-R22.5) | 2,550 mm (standard tires) (8' 4'') |
Width (600/50-R22.5) | 2,750 mm (optional tires) (9' 1'') |
Width (710/40-R22.5) | 2,950 mm (optional tires) (9' 7'') |
Width with drive axle | 2,690 mm |
Weight | 5,580 kg (12,300 lbs) |
Bale diameter | 1.25 m (48") |
Required Connections
Load Sensing connection (for LS mode) or one pressure connection and one depressurized return for the supply of the round baler |
Electrical power supply to the machine via ISOBUS connector or the included wiring harness |
7-pin power outlet for the entire lighting system, excluding work lights |
Power Requirement of the towing vehicle
Oil requirement | starting at 40 l/min at 200 bar optimal: starting at 65 l/min at 200 bar |
Power requirement | at least 90 kW |
Additional Equipment
Width altered to 2,770 mm | With drive axle: Width altered to 2,890 mm
Width altered to 2,970 mm
A bale ramp can be used to deposit the bale outside of the swivel range of the tailgate. Resetting the machine is not necessary.
Allows for easier bale dropping in slope positions.
Attention! Cannot be used in combination with the bale ramp.
2 cameras for monitoring binding and bale deposit, including color monitor
The bale is wrapped simultaneously in two nets or wide films.
This cuts the binding time for the bale in half.
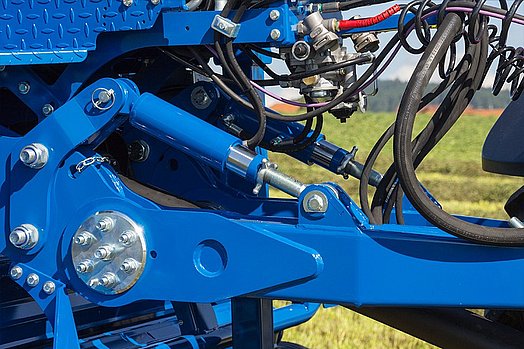
Hydraulic articulated drawbar with two double-acting cylinders
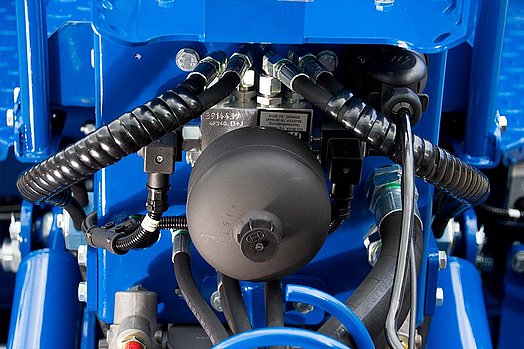
Hydraulic articulated drawbar affords the operator an exceptionally smooth ride
- Hydraulic drive uphill
- Automatic braking function downhill
- ABS system
- Automatic regulation
- Parameters can be set on the terminal
Only in combination with tires 500/60-R22.5 and 600/50-R22.5
with 8 buttons and encoder
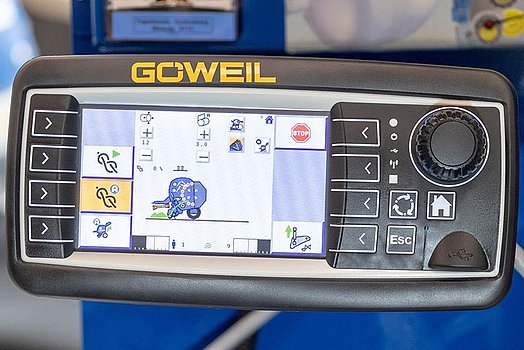
with 12 buttons and encoder
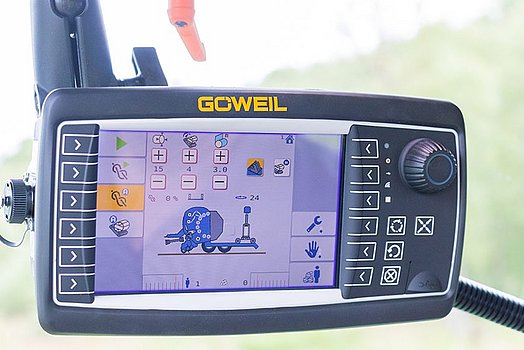
Wiring harness is required if ISOBUS is not available on the tractor
2 cameras for monitoring binding and bale deposit, including color monitor
Consisting of
- Dosistar control unit
- Pump with filter
- Electronic flow meter
- Various nozzles
- 100 l tank
Consisting of compressed air hose and air gun, used for cleaning the round baler.